In the world of industrial innovation, where precision meets performance, the right tools define success. Whether you're testing cutting-edge electric motors, optimizing energy efficiency, or fine-tuning mechanical systems, hysteresis-based technologies and motor test equipment stand as unsung heroes. Let’s explore how these engineering marvels—hysteresis brakes, dynamometers, clutches, and integrated motor test systems—are reshaping industries from automotive to renewable energy.
---
### 🌟 The Magic of Hysteresis: A Silent Revolution
Hysteresis technology harnesses the power of magnetic fields to deliver unparalleled control. Unlike BLDC motor durability systems -based systems, hysteresis devices operate contact-free, eliminating wear and tear while maintaining consistent torque. Imagine a brake that never degrades, a dynamometer that measures power with zero slippage, or a clutch that transfers energy seamlessly—this is the promise of hysteresis.
**Hysteresis Brakes**:
From aerospace components to robotics, hysteresis brakes provide smooth, adjustable torque without physical contact. Their maintenance-free design makes them ideal for applications demanding longevity, such as tension control in manufacturing or precision positioning in medical devices.
**Hysteresis Dynamometers**:
Testing motors? Say goodbye to inaccuracies. These dynamometers absorb and measure power with surgical precision, whether you’re evaluating EV drivetrains or industrial pumps. Their ability to simulate real-world loads ensures reliable data for R\u0026D teams pushing the boundaries of efficiency.
**Hysteresis Clutches**:
Need torque control without backlash? Hysteresis clutches offer slip-free power transmission, perfect for packaging machinery, printing presses, or even wind turbines. Their silent operation and durability reduce downtime, keeping production lines humming.
---
### ⚡ Motor Test Systems: Where Science Meets Scalability
Modern motor testing isn’t just about “does it work?”—it’s about optimizing every watt. Advanced motor test systems integrate hysteresis dynamometers, data acquisition modules, and AI-driven analytics to deliver insights that drive innovation.
**Key Features of Next-Gen Test Systems**:
- **Adaptive Load Simulation**: Mimic real-world conditions, from sudden torque spikes to steady-state operation.
- **Energy Recovery**: Capture wasted energy during testing and feed it back to the grid, slashing costs and carbon footprints.
- **Modular Design**: Scale your setup for anything from micro-motors in drones to gigawatt-scale turbines.
Case in point: A leading EV manufacturer reduced prototype testing time by 40% using a hysteresis-based dynamometer system, accelerating their time-to-market while ensuring regulatory compliance.
---
### 🏭 Industry Applications: Beyond the Lab
1. **Automotive**: Validate hybrid powertrains, test regenerative braking systems, and optimize battery performance.
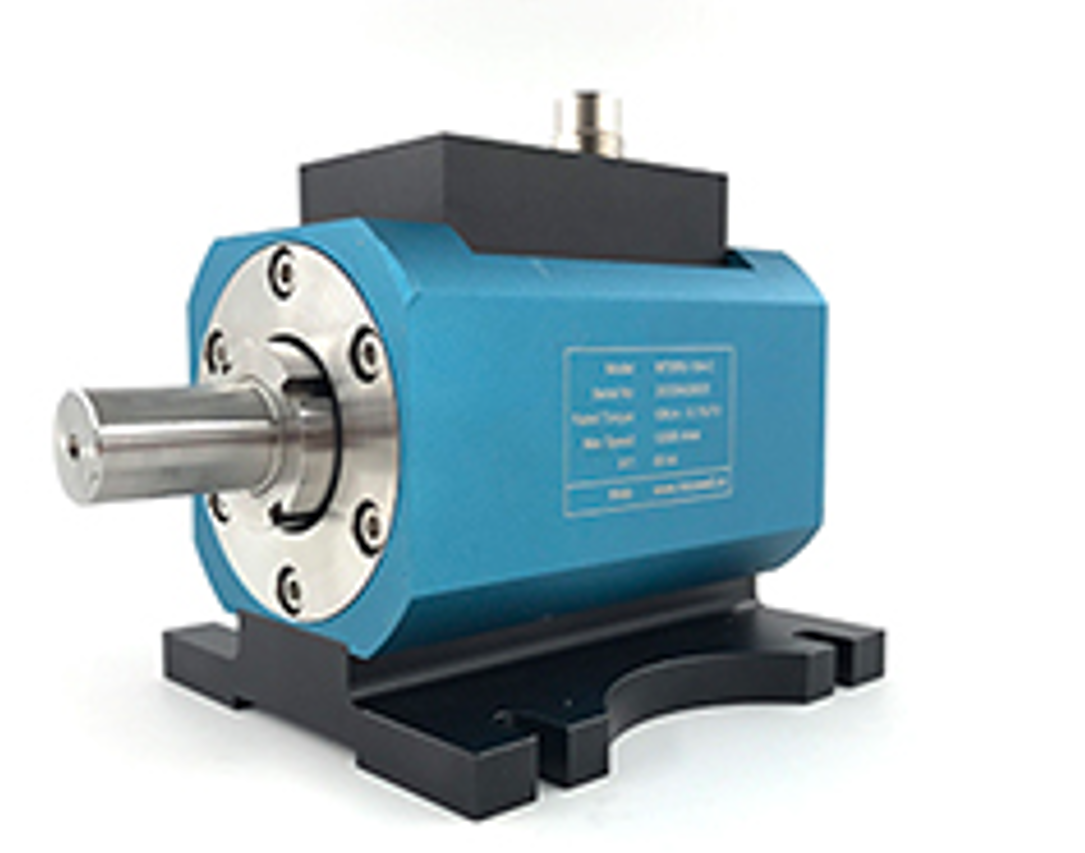
2. **Aerospace**: Ensure reliability of actuation systems and auxiliary power units under extreme conditions.
3. **Renewables**: Stress-test wind turbine generators and solar tracking motors to withstand decades of operation.
4. **Consumer Electronics**: Perfect the torque profile of smartphone vibration motors or drone propellers.
A wind farm operator recently shared: “With hysteresis dynamometers, we’ve cut generator validation time by half. Now, we deploy turbines faster without compromising on lifespan.”
---
### 🔍 Why Choose Hysteresis Over Conventional Systems?
- **Zero Maintenance**: No brushes, no friction pads—just magnetic fields doing the work.
- **Silent Operation**: Ideal for noise-sensitive environments like hospitals or R\u0026D labs.
- **Linear Torque Control**: Adjust output instantly via current control, enabling dynamic testing scenarios.
Traditional friction brakes? They’re like using a sledgehammer for a job that requires a scalpel.
---
### 📈 Future-Proofing with Smart Motor Test Equipment
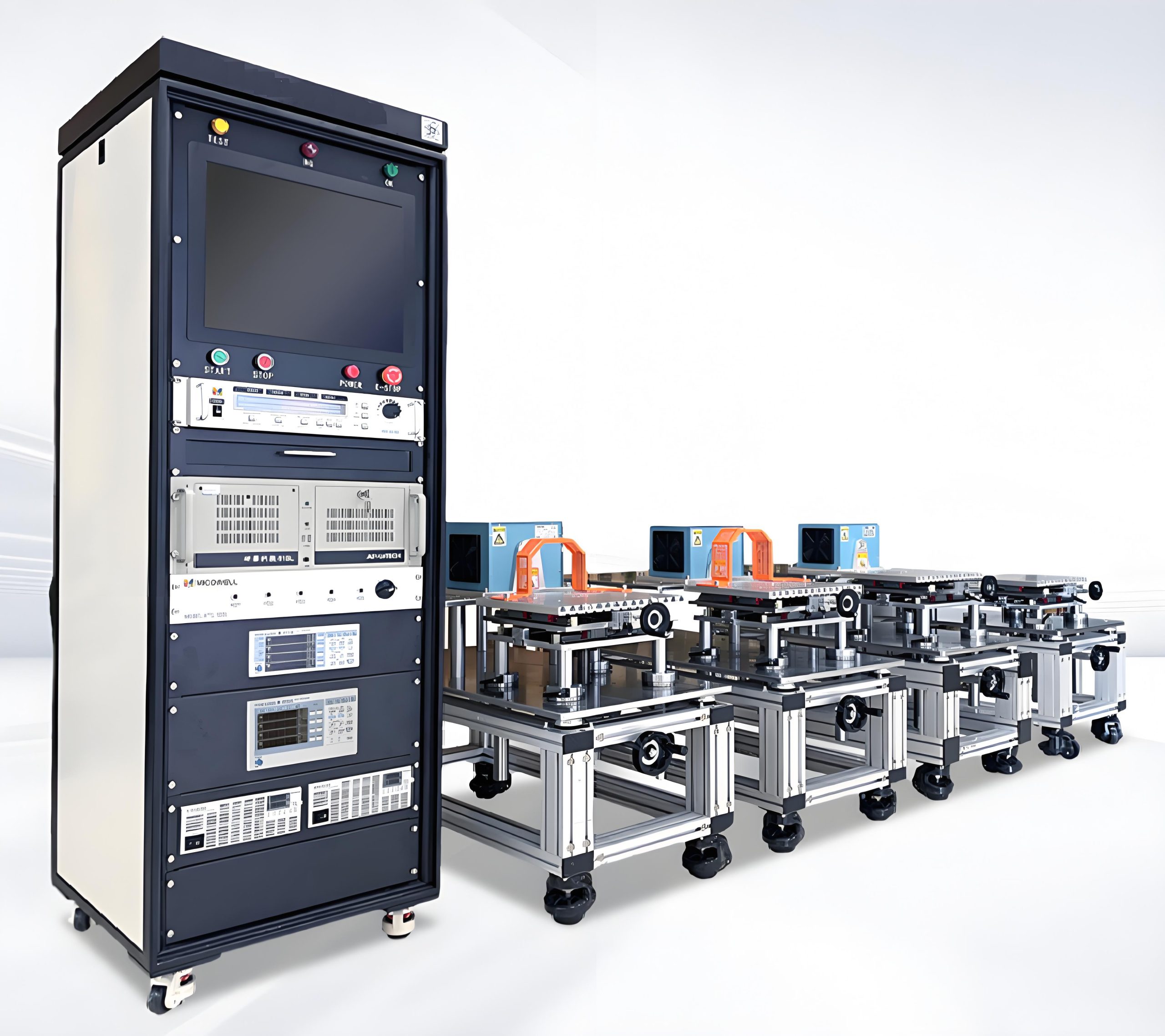
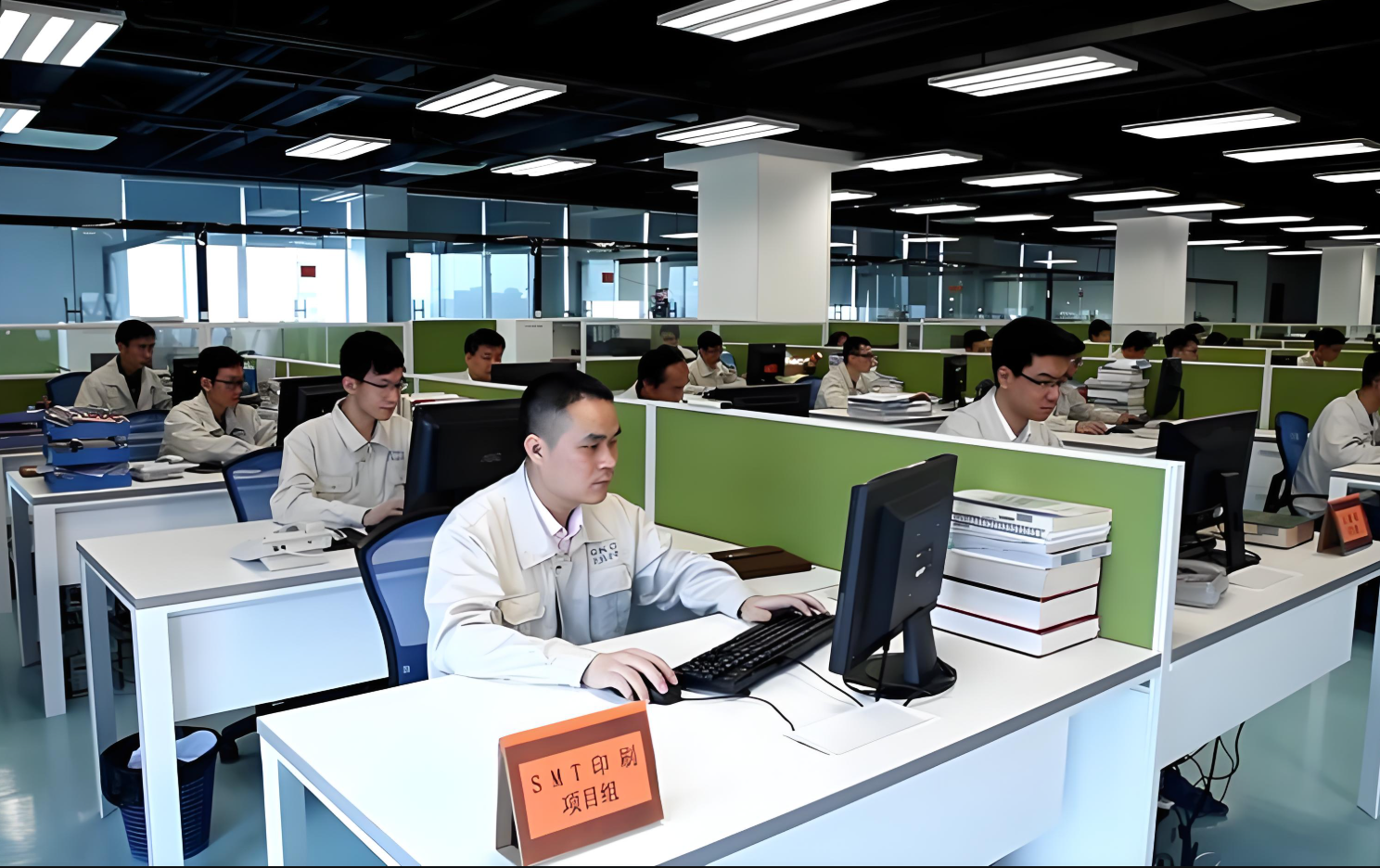
The rise of IoT and Industry 4.0 has transformed testing from a standalone process into a data goldmine. Modern systems now offer:
- **Predictive Analytics**: Spot motor degradation patterns before failures occur.
- **Remote Monitoring**: Control tests from across the globe via cloud interfaces.
- **AI-Optimized Workflows**: Automate test sequences based on real-time performance data.
Imagine a world where your test equipment learns from every experiment, continuously refining testing protocols. That’s not sci-fi—it’s happening now.
---
### 🛠️ Choosing the Right Partner: Quality Matters
Not all hysteresis systems are created equal. Look for:
- ISO-certified calibration
- Customizable software interfaces
- Global technical support networks
A European robotics company learned this the hard way: After switching to a low-cost imitation dynamometer, they faced inconsistent readings that delayed a product launch. They’ve since partnered with specialists offering traceable certifications and 24/7 support.
---
### 🌍 Sustainability at the Core
Hysteresis systems aren’t just efficient—they’re green. By enabling accurate energy recovery and reducing material waste (thanks to their non-contact design), they align with global sustainability goals. One automotive supplier reported a 15% reduction in energy costs after upgrading to regenerative motor test benches.
---
### 🔮 The Road Ahead: Electrification and Beyond
As industries pivot toward electrification, the demand for precise motor testing will skyrocket. Hysteresis technology, with its blend of reliability and adaptability, is poised to become the backbone of smart manufacturing and clean energy transitions.
From hypercars to hydroelectric plants, the message is clear: If you’re not leveraging advanced hysteresis systems and motor test solutions, you’re not just falling behind—you’re leaving performance and profits on the table.
---
Ready to redefine what’s possible? The future of precision engineering starts here. 🚀