In the rapidly evolving world of industrial automation and precision engineering, the demand for reliable, high-performance testing and control systems has never been greater. Whether you’re developing cutting-edge electric vehicles, optimizing aerospace components, or pushing the boundaries of robotics, the tools you use to validate performance can make or break your success. Enter hysteresis brakes, dynamometers, clutches, and motor testing systems—technologies that are quietly powering the next generation of innovation.
━━━━━━━━━━━━━━━━━━
**The Science Behind Hysteresis: A Silent Powerhouse**
At the heart of these systems lies the principle of hysteresis—a phenomenon where materials resist changes in magnetization. Unlike friction-based mechanisms, hysteresis devices operate without physical contact, reducing wear and tear while delivering unparalleled precision. Imagine a braking system that adjusts torque with micrometer-level accuracy or a dynamometer that simulates real-world loads without mechanical degradation. This is the magic of hysteresis.
━━━━━━━━━━━━━━━━━━
**Hysteresis Brakes: Where Control Meets Durability**
🛠️ Traditional brakes rely on friction, which leads to heat generation and component erosion. Hysteresis brakes, however, use magnetic fields to create resistance. This means:
- Zero contact between components, eliminating friction-induced wear.
- Consistent torque output across varying speeds.
- Silent operation—perfect for noise-sensitive environments like labs or medical devices.
Motor efficiency testing from renewable energy (testing wind turbine generators) to automotive (evaluating EV drivetrains) are adopting these brakes for their longevity and precision.
━━━━━━━━━━━━━━━━━━
**Hysteresis Dynamometers: The Ultimate Testing Partner**
⚡ When it comes to measuring power, torque, or efficiency, hysteresis dynamometers are game-changers. Their ability to provide dynamic load simulation makes them ideal for:
- Validating electric motors under fluctuating conditions.
- Testing hybrid vehicle transmissions.
- Quality assurance in industrial pump manufacturing.
A major aerospace manufacturer recently credited hysteresis dynamometers for slashing testing time by 40% during jet engine R\u0026D—proof that smarter tools yield faster breakthroughs.
━━━━━━━━━━━━━━━━━━
**Motor Test Systems: Beyond Basic Validation**
Modern motor test equipment isn’t just about “pass or fail.” It’s about capturing granular data to refine designs. Advanced systems now integrate:
- Real-time thermal imaging to prevent overheating.
- AI-driven analytics for predictive maintenance insights.
- Customizable software interfaces compatible with IoT platforms.
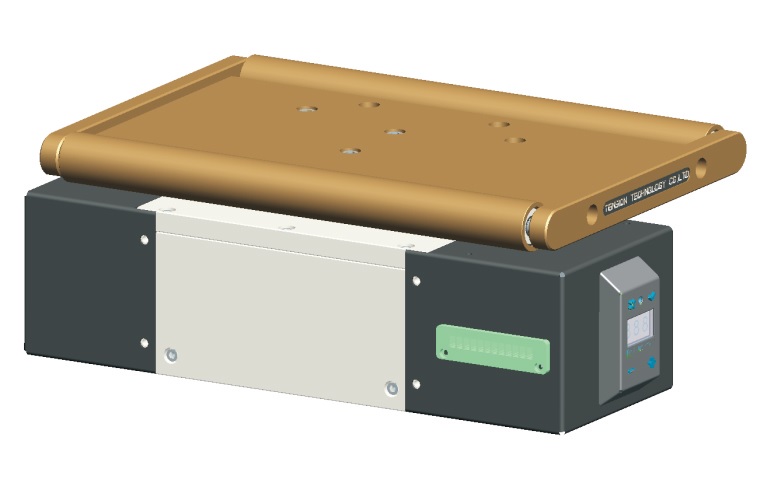
For example, a robotics startup used a motor test system to identify inefficiencies in their servo motors, boosting battery life by 22%—a critical edge in competitive markets.
━━━━━━━━━━━━━━━━━━
**Hysteresis Clutches: Smooth Transitions, Seamless Results**
🔧 In applications requiring controlled engagement—think packaging machinery or precision conveyors—hysteresis clutches offer smooth torque transfer without jerks or slippage. Benefits include:
- Adjustable torque limits to protect delicate components.
- Maintenance-free operation due to non-contact design.
- Energy efficiency, as power is only consumed during activation.
A food processing plant reported a 30% reduction in product waste after switching to hysteresis clutches, citing improved handling of fragile items.
━━━━━━━━━━━━━━━━━━
**The Human Factor: Why Expertise Matters**
Even the most advanced systems require human insight. Leading providers now combine hardware with hands-on support:
- On-site calibration services.
- Training programs for engineers.
- 24/7 remote diagnostics.
One client in the electric vehicle sector praised their vendor’s team for troubleshooting a torque inconsistency issue in under three hours—saving a weeks-long production delay.
━━━━━━━━━━━━━━━━━━
**Sustainability Through Innovation**
🌱 As industries face pressure to reduce carbon footprints, hysteresis-based systems answer the call. Their energy-efficient operation and long lifespan minimize waste. For instance, a wind energy company cut annual maintenance costs by $200,000 by replacing hydraulic brakes with hysteresis models in their turbines.
━━━━━━━━━━━━━━━━━━
**Looking Ahead: The Road to Industry 5.0**
With the rise of smart factories and autonomous systems, the integration of hysteresis devices with IoT and machine learning will redefine testing standards. Imagine a dynamometer that automatically adjusts test parameters based on live data or a clutch that learns usage patterns to optimize performance.
━━━━━━━━━━━━━━━━━━
**Your Next Move**
In a world where margins for error are shrinking, settling for outdated testing solutions isn’t an option. Whether you’re fine-tuning a drone’s propulsion system or ensuring the reliability of life-saving medical equipment, hysteresis technologies offer the precision, durability, and intelligence needed to stay ahead.
The question isn’t whether you can afford to upgrade—it’s whether you can afford not to.
[Contact us today to explore how our hysteresis brakes, dynamometers, and motor testing solutions can transform your workflows. Let’s build the future, one precise measurement at a time.]
━━━━━━━━━━━━━━━━━━
*Innovate. Test. Excel.* 🔧📊🚀